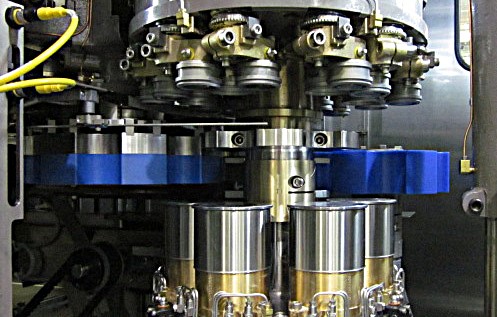
CONTINENTAL Can Seaming Machines
CONTINENTAL 2000 Series seamers serve a wide range of canning applications, able to handle can diameters from 202 to 610 and speeds up to 1200 Cans Per Minute (CPM). Continental seamers are also designed to manufacture cans and are considered the gold standard in many can-making plants today. These seamers can operate as either a random infeed configuration, accepting cans from an indpendent filler, or pitch-matched and synchronized to a filling machine. Both connections leverage a horizontal feed chain to ensure proper timing of the can to the seaming head. Our three-screw cover feed provides optimum lid separation and control of all end types.
Discover our Continental can seamer solutions.
The CONTINENTAL can seamer is designed for quick changeover times for both body and lid, and is simple to run and maintain. It is a grease-lubricated seamer, delivers superior seam quality, and offers industry-leading longevity for reliable operation.
About CONTINENTAL Can Seaming Machines
How does a Seamer work?
The objective of a Can Seamer machine is to create an airtight - or hermetic - seal between the can body and the can end (or lid) to create a secure, leak-proof closure to preserve the product and extend its shelf life. This process is referred to as double seaming, first pioneered and patented by the Angelus Can Machine Company more than a century ago.
In the process of double seaming, a metal-to-metal or metal-to-composit joint is formed by interlocking five layers: three from the can end and two from the can body. These layers are compressed and tightly ironed to form the hermetic seal.
How does Filler/Seamer integration work?
Our Seaming Machines are designed to function either as stand-alone machines or integrated with a Filler in food, beverage, home and personal care, chemical, and pharmaceutical production lines.
When the Seamer is in a stand-alone configuration, it is referred to as Random Infeed. In this case, the seamer is equipped with its own base-driven motor and is not synchronized with the filler turret. Filled cans travel to the seamer either from an independent filler or from an accumulation table. The seamer is equipped with a timing feedscrew which is calibrated to separate the cans according to the timing of the seamer feed chain, which then drives the cans into the seaming turret, where they are then hermetically sealed.
When the Seamer is connected to a filler, the filler must have a compatible pitch to match the seamer. Connection happens in one of two ways: mechanical or servo synchronization. In a mechanical connection, the seamer drives the filler via one motor, using a filler belt drive system and the filler and seamer are connected via a drive shaft assembly. In the case of servo synchroization, the filler and seamer are electronically synchronized via separate servo motors on each machine. One servo motor follows the other through encoder communication. This synchronization ensures the correct speed alignment between the two machines.