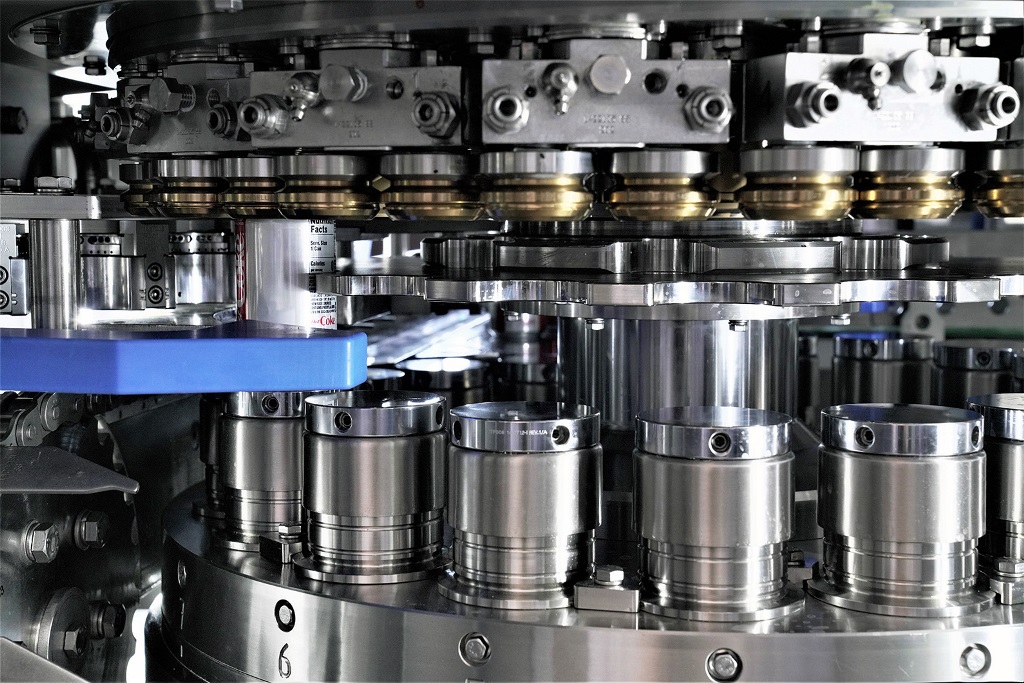
ANGELUS Can Seaming Machines
ANGELUS seamers have earned their reputation as the industry standard for quality and reliability in a wide variety of Food and Beverage applications, as well as a full spectrum of industries from Chemical, to Home and Personal Care, to Pharmaceuticals and more. Built to last and supported by expert service and support, spare parts, and training, the Angelus name has become synonymous with longevity and performance. Our passion for seaming technology drives us to lead with innovative designs that deliver best-in-class seam integrity, hygienic design, fast and reliable changeover, and superior lightweight can handling to help you get the most from your seamer investment.
Discover our can seamer solutions.
ANGELUS seamers span two product lines: Angelus Legacy seamers and Angelus V-Series seamers. The Angelus Legacy line is known for its trusted performance and long-term reliability, with many machines installed more than 60 years ago still in active production in the field. The V-Series line builds upon this strong foundation, retaining all of the rugged design and dependability, while adding innovations to enhance ease of maintenance, lower the cost of ownership, and deliver patented innovations for lightweight can handling.
V-Series seamers contain 25% fewer components than Angelus Legacy machines and employ an 80% parts commonality across the family. In addition, the metric base-driven design is built with the ideal pitch match to pair with today's modern fillers, and the 304 stainless steel used in all product contact areas ensures a clean, sanitary design that is foam and chemical cleaning-compatible. This series can be used for atmospheric, under cover gassing, steam vacuum, and liquid Nitrogen dosing applications.
About ANGELUS Can Seaming Machines
How does a Seamer work?
The objective of a Can Seamer machine is to create an airtight - or hermetic - seal between the can body and the can end (or lid) to create a secure, leak-proof closure to preserve the product and extend its shelf life. This process is referred to as double seaming, first pioneered and patented by the Angelus Can Machine Company more than a century ago.
In the process of double seaming, a metal-to-metal or metal-to-composit joint is formed by interlocking five layers: three from the can end and two from the can body. These layers are compressed and tightly ironed to form the hermetic seal.
ANGELUS V-SERIES portfolio, technical data
Model | Speed Range | Seaming Stations | Stainless Steel | Lubrification | Can Diameter | Can Height | Can Pitch | Application |
---|---|---|---|---|---|---|---|---|
18V | 500 - 2,500 | 18 | Standard | Oil Recirculation | 200 - 300 in 50.8 - 76.2 mm | 113 - 800 in 46.0 - 203.3 mm | 3.563 or 3.666 in 90.5 - 93.1 mm | Beverage |
12V | 400 - 1,800 | 12 | Standard | Oil Recirculation | 200 - 300 in 50.8 - 76.2 mm | 113 - 800 in 46.0 - 203.3 mm | 3.563 or 3.666 in 90.5 - 93.1 mm | Beverage |
8V | 250 - 1,000 | 8 | Standard | Oil Recirculation | 200 - 300 in 50.8 - 76.2 mm | 113 - 800 in 46.0 - 203.3 mm | 3.876 in 98;45 mm | Food & Beverage |
6V | 175 - 1,000 | 6 | Standard | Oil Recirculation | 200 - 401 in 50.8 - 103.2 mm | 113 - 800 in 46.0 - 203.3 mm | 5.168 in 131.27 mm | Food & Beverage |
4V | 100 - 450 | 4 | Standard | Oil Recirculation | 200 - 401 in 50.8 - 103.2 mm | 113 - 800 in 46.0 - 203.3 mm | 6.46 in 164.08 mm | Food & Beverage |
3V | 75 - 350 | 3 | Standard | Oil Recirculation | 401 - 603 in 103.2 - 157.2 mm | 113 - 910 in 41.3 - 244.5 mm | 10.336 in 262.53 mm | Food & Beverage |
How does Filler/Seamer integration work?
Our Seaming Machines are designed to function either as stand-alone machines or integrated with a Filler in food, beverage, home and personal care, chemical, and pharmaceutical production lines.
When the Seamer is in a stand-alone configuration, it is referred to as Random Infeed. In this case, the seamer is equipped with its own base-driven motor and is not synchronized with the filler turret. Filled cans travel to the seamer either from an independent filler or from an accumulation table. The seamer is equipped with a timing feedscrew which is calibrated to separate the cans according to the timing of the seamer feed chain, which then drives the cans into the seaming turret, where they are then hermetically sealed.
When the Seamer is connected to a filler, the filler must have a compatible pitch to match the seamer. Connection happens in one of two ways: mechanical or servo synchronization. In a mechanical connection, the seamer drives the filler via one motor, using a filler belt drive system and the filler and seamer are connected via a drive shaft assembly. In the case of servo synchroization, the filler and seamer are electronically synchronized via separate servo motors on each machine. One servo motor follows the other through encoder communication. This synchronization ensures the correct speed alignment between the two machines.